The total station is topographic instrument used for indirect surveying. The instrument consists of an electronic distance meter, an electronic goniometer for measuring the azimuth angle, and a second electronic goniometer for measuring the zenith angle. The calculation of the data stored during the campaign phase, are stored through a computer with a user interface. The total station, therefore, can take angle and distance measurements of a series of points and determine their exact spatial location with respect to a predefined coordinate system.
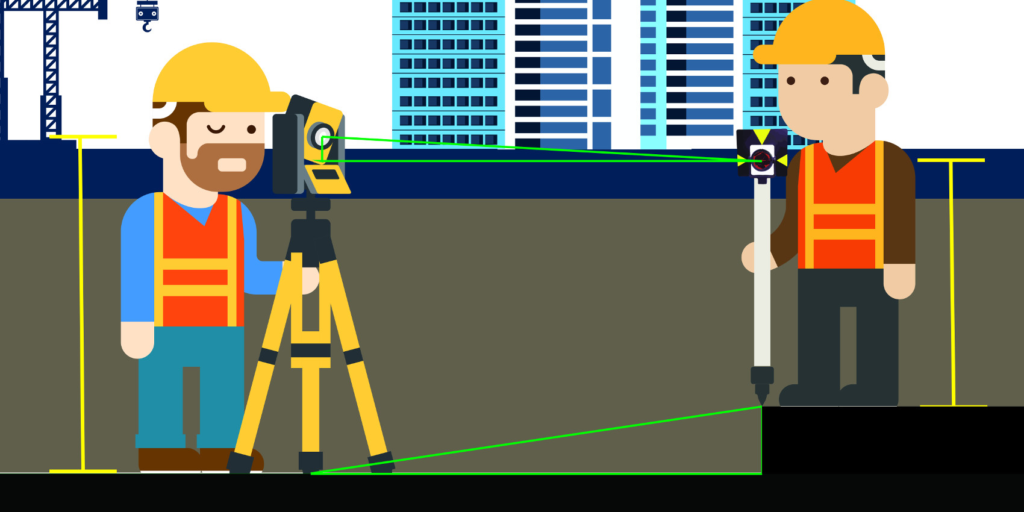
In order to carry out a total station survey correctly, the Stationing phase must be performed correctly.
Stationing determines from the beginning the correct measurement of the points, it consists of placing the total station on the vertical of a materialized point usually with a nail securing it to the tripod by means of a clamping screw. The fixing is done by straddling the point with the head horizontal while keeping the tripod legs extended momentarily free to fix them better in the ground, thus creating the stability to proceed to the surveying phase. The total station and laser lead are turned on. The latter consists of a red laser light that shows the point on which the instrument is plumb, so for proper stationing this laser must center the station nail while the instrument is perfectly level. Having verified this, the instrument is positioned and it is possible to set the zero angle to a reference (another station nail for example) by an operation called “zeroing.”
The measurement through the Total Station takes into account vertical angles, horizontal angles and inclined distance and can be exported from the instrument in raw Polar coordinates or in Cartesian coordinates. In the former case, the surveyor will be able to intervene independently in error checking and polygonal construction; in the latter case, the instrument and its internal and external software will be trusted.
For correct angular and linear measurement, it is necessary to center each point with the scope until it is displayed exactly on the intersection of lines corresponding to the optical center of the lens.
Distance is detected using the Electronic Distance Measurement (EDM) technology built into the Total Station. This system simply detects the time it takes for the laser beam to travel to and from the hit point to the telescope. The data is stored by the instrument, and at the same time the polar coordinates are shown via display.
Measurement with the Total Station can be done through two methodologies:
- infrared beam
- laser beam
Surveying through the infrared beam needs a reflective system; in this case a prism or mini prism is used for measurement to further mitigate the detection error.
Laser beam surveying, on the other hand, is a method adopted to survey points that are difficult for the operator to access, since no reflective system needs to be placed with laser.
The traditional Total Station in recent times has evolved into the Motorized or Robotic Total Station. Such an instrument allows the operator to be able to work even without a partner since it independently targets the moving prism. In addition, such an instrument can also activate a wide-field search procedure, capable of realigning the reticle to the prism if it loses it totally. One of the interesting features in the use of Total Motorized Stations is self-centering for the zeroing and measuring phase of stations: through the use of this feature, human centering error is mitigated.